超電導フライホイール蓄電装置
超電導フライホイール蓄電装置とは、余剰電力で、フライホイールを回し、物理エネルギーとして蓄え、電気が必要な時には、フライホイールの回転力で発電して利用するというもの。つまり、バッテリーとして機能すると考えていい。
そのため、「メカニカルバッテリー」、「キネティック(Kinetic:運動による)バッテリー」とも呼ばれる。
太陽光発電、風力発電といった再生可能エネルギーの普及が進む中、アンシラリー用途(電力品質(周波数や電圧)の安定)として、「フライホイール蓄電」は、欧米を中心に注目を集めている。
用途は、アンシラリーをはじめ重化学工業、自動車、鉄道など様々。
国内では、1988年8月、京浜急行電鉄が逗子線神武寺駅 - 新逗子駅間にある逗子フライホイールポストに25キロワット時・3,000キロワットのものを設置して、鉄道の回生電力を貯蔵して有効活用するために用いている。これにより回生電力の12パーセントの再利用を可能にしている。
沖縄電力は、2009年に波照間島に可倒式風力発電設備とともにフライホイールを導入。フライホイールの出力は30kWで、合計8基設置。
自動車レースのF1では、2009年シーズンのレギュレーションから、運動エネルギー回生システム(KERS:Kinetic energy recovery system)が導入され、多くのチームはバッテリーにエネルギーを充電する電気式KERSを採用したが、ウィリアムズは、フライホイールを利用する機械式KERSを採用した。
結局、パッケージングの都合からバッテリー式に変更したが、システムは耐久レースのアウディ・R18 e-torn クワトロに転用され、2012年のル・マン24時間レースにおいて、ハイブリッドカー初の総合優勝に繋がった。
ただし、このシステムは、一度電気に変換し、モーターでフライホイールを回転させるのではなく、機械的に回転エネルギーを入出力させる。
フライホイール蓄電が脚光を浴びる理由は、ランニングコスト。
リチウムイオン電池(LiB)の充放電回数、1000〜2000回(自動車向けで5000〜7000回)に対し、フライホイール蓄電は、20万回以上を実現する。
重いフライホイールを、高回転で回すほど蓄電量が増えるのだが、重いモノを高速回転させるのは非常に危険である。
よって、強度の高い、CFRP(カーボンファイバー強化プラスチック)製のフライホイールが用いられる。
そんな中、我が国では、世界最大級の超電導フライホイール蓄電システムの試運転が開始された。
古河電気工業(株)、(財)鉄道総合研究所、クボテック(株)等、数社は、共同で世界最大級の超電導フライホイール蓄電システム実証機を完成。
今年度(2015)夏頃より、山梨県米倉山の山梨県メガソーラー発電所、及び、東京電力の系統に接続し、変動の大きい再生可能エネルギーの安定導入に向けての実証試験を開始予定とのこと。
このシステムは、フライホイールを超伝導磁気軸受けによって、非接触で浮上させ、軸受けの磨耗損失をゼロとすることで運転効率を向上させる。
重いフライホイールを使用することができるため、大幅な高エネルギー密度化が可能になるほか、非接触であるため軸受けの寿命を半永久に延ばすことができ、メンテナンスフリーとなる。
フライホイールは、クライオスタットと呼ばれる真空容器に入れられる。
容器を真空に保つのは、フライホイールの空気抵抗を抑えるためである。
従来の超電導フライホイールでは、超伝導部分は固定側だけに用い、回転側は永久磁石を使用して来た。これでは、超伝導のメリットを生かしきれないため、今回は回転側にも超伝導を用いる構造としている。
軸受け(固定側)には、超伝導コイルを、回転軸には超伝導バルク体を、軸下部と、軸中間部に配置(画像下)。
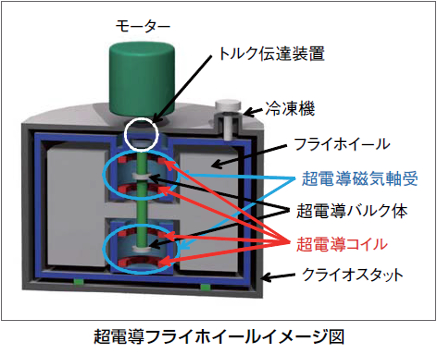
超伝導コイルとは、超低温に冷やすことで大量の電流を流す事のできる「超伝導線材」を巻いて作ったコイルで、超伝導バルク体とは、超伝導物質の塊である。
超伝導バルク体は、超伝導コイルの磁場の中に配置すると、反発する性質があるため、冷却した超伝導コイルに通電すると、フライホイールは、径方向、軸方向共に非接触浮上支持される。つまり、完全に空中に浮かんだ状態となる。
超伝導磁気軸受は、大荷重にも耐えられるため、従来よりも高い総エネルギー密度にできる。ただし、フライホイール全体をクライオスタットに入れ、超伝導部分を冷却する必要がある。
フライホイールへのエネルギーの伝達は、永久磁石カップリングを用いたトルク伝達装置で行う。つまり、フライホイールは外部との接触無しに回転し、エネルギーの出し入れを行うのだ。
従来のCFRP製フライホイールは、直径1m前後が限界だったが、炭素繊維の織り方を工夫することで、高強度、高信頼性を実現し、直径2mの大径化に成功。今回の実証機では、これを9枚接着し、高さ90pにしたものを使用している(画像上)。
超伝導磁気軸受は、第2世代高温超伝導材を用いた高強度高温超伝導マグネットを使用。50K(−253℃)以下まで冷却し、約4トンのフライホイールを非接触で支持する。
また、従来の20K(−223℃)に比べ、大幅な高温での運転が可能になり、冷却コストの低減が図られている。
今回完成した実証機は、直径2m、重さ約4トンのフライホイールを、最大6000rpmで回転させ、出力300kw、蓄電容量100kwが得られる世界最大級の蓄電システムである。